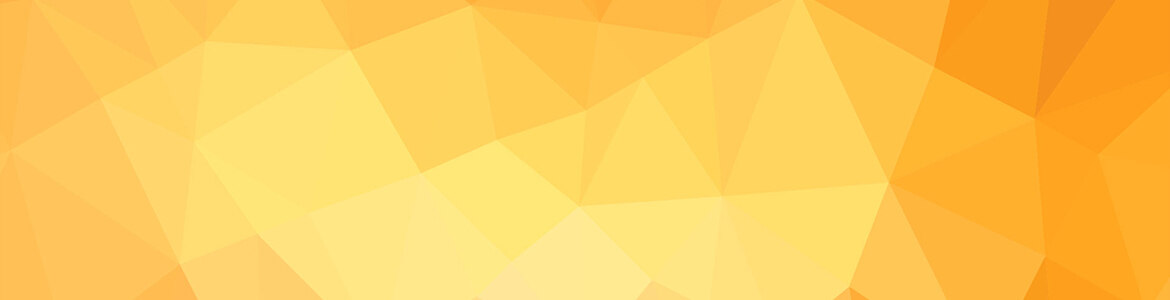
Eroz Environ Engineer Pvt. Ltd. - | E-Showroom
Eroz Environ Engineer Pvt. Ltd. - | E-Showroom
Mini Blast Furnace (Mandir Bhatti) with Air Pollution Control Device
 About Mini Blast FurnaceÂ
A Mini Blast Furnace (commonly known as Mandir Bhatti or Shahi Bhatti) is a simple, time-tested and widely used system to produce secondary lead in India and many other countries. It is the most basic of all furnaces and a production system based on this technology has certain distinct characteristics such as:Â
Low Project Capital Cost Low Energy Cost (wooden coke fired) Easy to install Easy to operate & maintain Production of low Antimony Lead (soft lead) at low temperature Generates high pollutionÂ
Description of Mini Blast FurnaceÂ
The Furnace itself is a modified blast furnace which consists of a brick lined structure with fire brick oven in the midst and a metal Exo-skeletal structure outside. Raw material & fuel (coke) is charged manually through the side metal doors fitted in the brick structure and air is provided from the FD fans provided at the back of the brick structure. Molten metal & slag is tapped at the pits made in front of the brick structure and flue gases are sucked from the top of the brick structure which is provided with a metallic hood.Â
A typical Double Oven Mini Blast Furnace has the following standard sizes & specifications:
Outside Dimensions of Brick Structure: 2400mm L x 1900mm W x 2400mm H No. of Ovens: 2 Nos. Oven Size Top Dia: 600mm Bottom Dia: 250mm Depth: 650mm No. of FD Fans: 2 Nos. (1 for each oven) FD Fan Capacity: 300cmh at 250mm of WGÂ No. of Charging Doors: 2 Nos. (1 for each oven) Charging Door Dimensions: 1100mm H x 650mm WÂ
Manufacturing Process:Â
Lead to be manufactured from Mini Blast Furnace is usually obtained from scrapped batteries. They are cut open or broken to segregate lead scrap, plastic and other materials from it. Lead scrap in the form of lead powder and plates etc. is charged in the furnace along with a proportionate charge of wooden coke. Thereafter the furnace is manually fired with the help of rags. FD Fan provides the necessary air required for combustion from the back of the furnace. Coke in the oven performs the functions of both, the fuel as well as a reducing agent for obtaining lead from its oxides charged in the form of lead plates & powder.Â
Temperature of the furnace is maintained at the desired level for approximately 30 minutes, after which molten lead along with slag flows out from the bottom of the oven into the outlet pit. Here slag is separated and molten lead is poured into Ingot Moulds. To maintain this, continuous charge of raw material and coke is maintained in the furnace.Â
This process leads to generation of flue gases which are toxic in nature and need appropriate and adequate Air Pollution Control System for their treatment.Â
Process Details for a typical Double Mini Blast Furnace:Â
Raw Material Charged: 700-800 kg/ hr. Fuel used : Wooden Coke Calorific Value of Fuel used : 4000-5000 kCal/ kg.Â
Fuel Consumed: 70-75 Kg/hr.
Air Provided for Process: Â 300 cmh
Lead Produced (1st charge): 300-350 kg/hr.
Flue Gas Generation: 8000-9000 cmhÂ
Advantages and Disadvantages of Mini Blast FurnaceÂ
Advantages
No consumables used other than Wooden Coke which is also used as Fuel Low Power Consumption Produces low Antimony Lead suitable for soft lead purposes Pollution can be controlled with minimum fugitive emissions Easy to install, operate & maintain
Disadvantages
Cannot recover 100% lead in the first operation Subsequent recovery of lead after first recovery consumes higher coke & manpower. Equipment cannot be scaled up for higher production capacities.Â
Air Pollution Control System for Mini Blast FurnaceÂ
Various types of lead present in used batteries, plates and paste of lead oxide are charged in the furnace. In addition to these, certain compounds of sulphur are also present in the batteries. When this material is heated in the presence of carbon, lead oxide is converted to lead. This conversion along with burning of fuel generates flue gases and fumes containing dust, dirt, oxides of lead, lead particles and other impurities etc.Â
Hence, to meet various goals of maintaining employees' health, for factory environments as well as regulatory requirements, it becomes imperative to get high end Air Pollution Control Systems to be installed with the Mini Blast Furnaces.Â
Characteristics of Air Pollution generated in Mini Blast FurnaceÂ
Dust: 8000-15000 mg / Nm3 Temperature: 100-120oC Gases: Traces of NOx, SO2 and COÂ
Discharge Characteristics required as per NormsÂ
Dust: Less than 50 mg / Nm3 Lead (Pb): Less than 10 mg / Nm3
Temperature: 60-90o C Gases: Traces of NOx , SO2 and COÂ
Selection of Technology for Air Pollution Control SystemÂ
Based on the parameters and the standards mentioned, the following technology is adopted for Air Pollution Control System in Mini Blast Furnace:
Details of Air Pollution Control Device with functionsÂ
Duct and BendsÂ
Ducts and Bends are required to convey flue gases from point of suction to final top of the chimney and connect various equipments like spark arrestor, gravity chamber, cyclone, bag house, ID Fan and chimney. All bends and reducers are aerodynamically designed and have provision for manhole cleaning mechanism.Â
Gravity ChamberÂ
It is a low pressure drop device which:
Involute CycloneÂ
Cyclone is used to remove medium size particles from flue gases stream. The treated flue gases are discharged from top and dust is collected at bottom.Â
Bag Filtration SystemÂ
It is used for final filtration of flue gases to remove fine dust particulate matter using Pulse Jet Technology. Treated gases from all the bags are collected at top of bag house and passed through the ID Fan to exhaust the same through chimney. The dust is collected at bottom of hopper and is discharged through Rotary Air Lock Valve.Â
ID FanÂ
ID Fan provides necessary driving force to convey flue gases from top of furnace to top of the chimney. The volume sucked overcome the total resistance offered by equipment and duct with the help of fluid horse power provided by ID Fan driven by suitable motor.
Stack (Chimney)Â
The generated gases are passed to atmosphere after treatment through chimney of suitable height and diameter.
 Wet Scrubber for Air Pollution Control DeviceÂ
A Wet Scrubber in the Air Pollution Control System is mandatory in India and many parts of the world. Wet Scrubber uses water to scrub clean the flue gases of any pollutant gases or particles that may remain after Bag Filtration System. The Scrubber therefore requires a pump, pipeline and a retention tank.Â
The size of the Scrubber depends upon the capacity of the system being installed. Flue gases are introduced in the body of the Scrubber from side and as they move up towards the top of the Scrubber which has the outlet, they pass through a spray of fine water droplets provided by a spray shower provided in the body. This fine spray leads to scrubbing of any pollutant in the flue gases. Cleaned gases escape through the top opening after passing through a mist eliminator whereas water with pollutants moves to the bottom of the Scrubber from where it is passed into the tank. One or more chambers of the tank allow for settling of pollutants which are then periodically cleaned and fresh water is added to make up any loss in quantity of water. It is then recirculated to the Scrubber.